Shaping Thermal Performance // Architectural Enclosures Graduate Course
Spring 2024
In the context of the climate crisis and rising temperatures, building enclosures must respond to a plurality of requirements –including thermal insulation, heat storage, ventilation, and solar radiation control -- ideally, with minimal embodied carbon and at low cost. While contemporary normative approaches tackle this with assemblies of highly specialized layers, alternative solutions emerge that use geometric specificity to integrate multiple high-performance behaviors in a humble and simplified material palette.
This new workshop explored the use of earthen construction as a low-carbon approach to a heat-resilient architecture that provides cooling solutions in a climate-specific way. The initial exercise challenged students to design a mug (a wall that separates two different environments) to be as lightweight as possible while keeping water cold for as long as possible. The final project consisted of designing an earthen-based wall system supported by digital simulations and physical experiments while exploring its potential impact on architectural expression through its application in a single-story house.
Teaching Team: Eduardo Gascón Alvarez and Caitlin Mueller with support from Professor Les Norford and PhD candidate Sandy Curth
Students: Akshata Atre, Rachel Blowes, Cheng-Hsin Chan, Aisha Cheema, Bryce Crawford, Natasha Hirt, Sylvia Jimenez, Mara Jovanovic, Minyoung Kim, Thomas King, Dong Nyung Lee, Yanyi Liu, Ashutosh Lohana, Patrick Margain, Ryan Otterson, Zhi Ray Wang
Images 1 to 5: Fabrication, firing, and testing of the 3D-printed ceramic mugs. Students experimented with the massing, material distribution, and air pocket location within their designs to achieve a minimal weight (kg) and maximum time constant (h), a measure of the mugs' combined insulation and heat storage properties.
Images 6 to 10: Earth-based wall systems designed for optimal passive cooling performance across three hot climates with varying conditions. The explored fabrication systems ranged from compressed earth blocks to prefabricated 3D-printed modules, multicellular fired clay blocks, on-site printed earth, and wattle and daub.


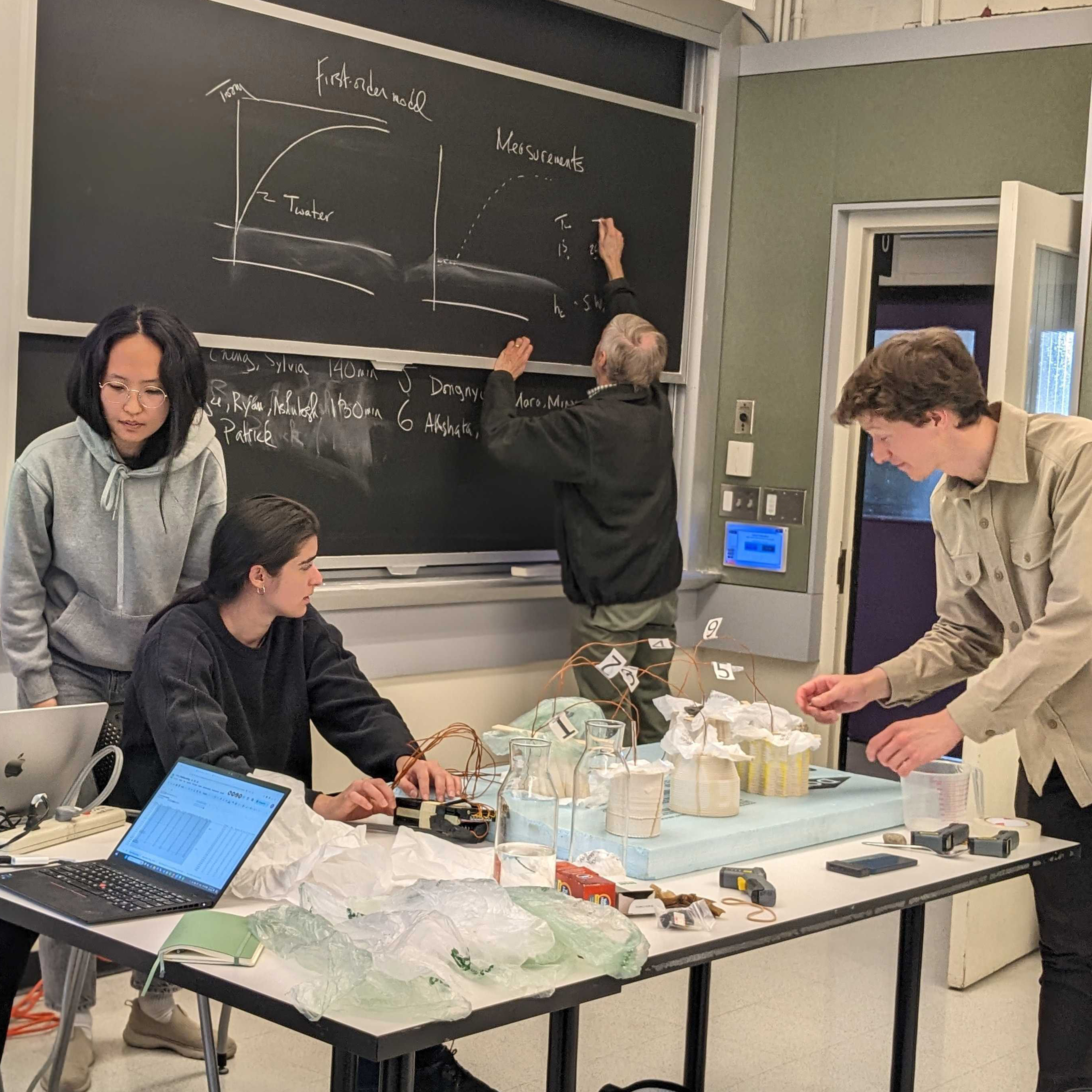
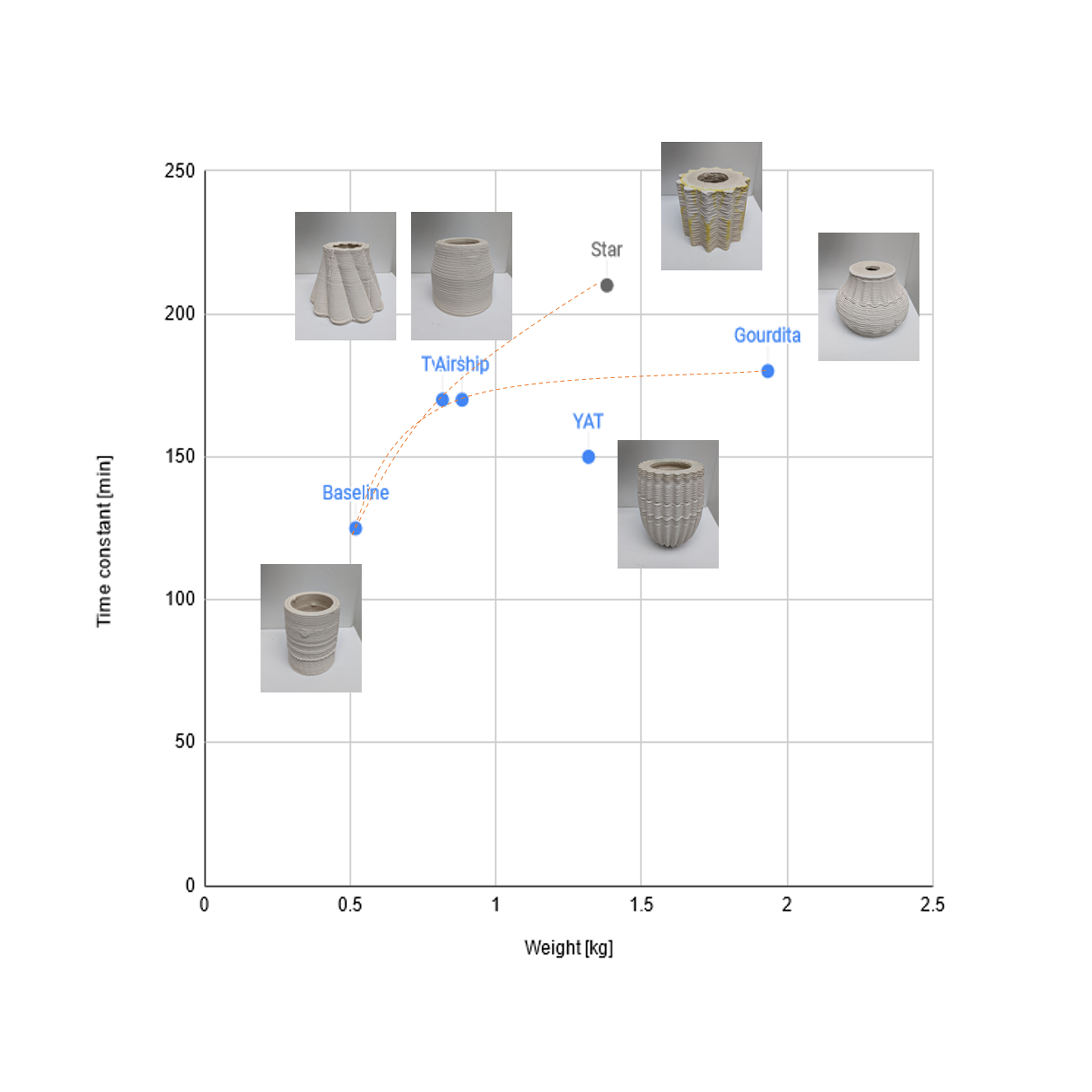




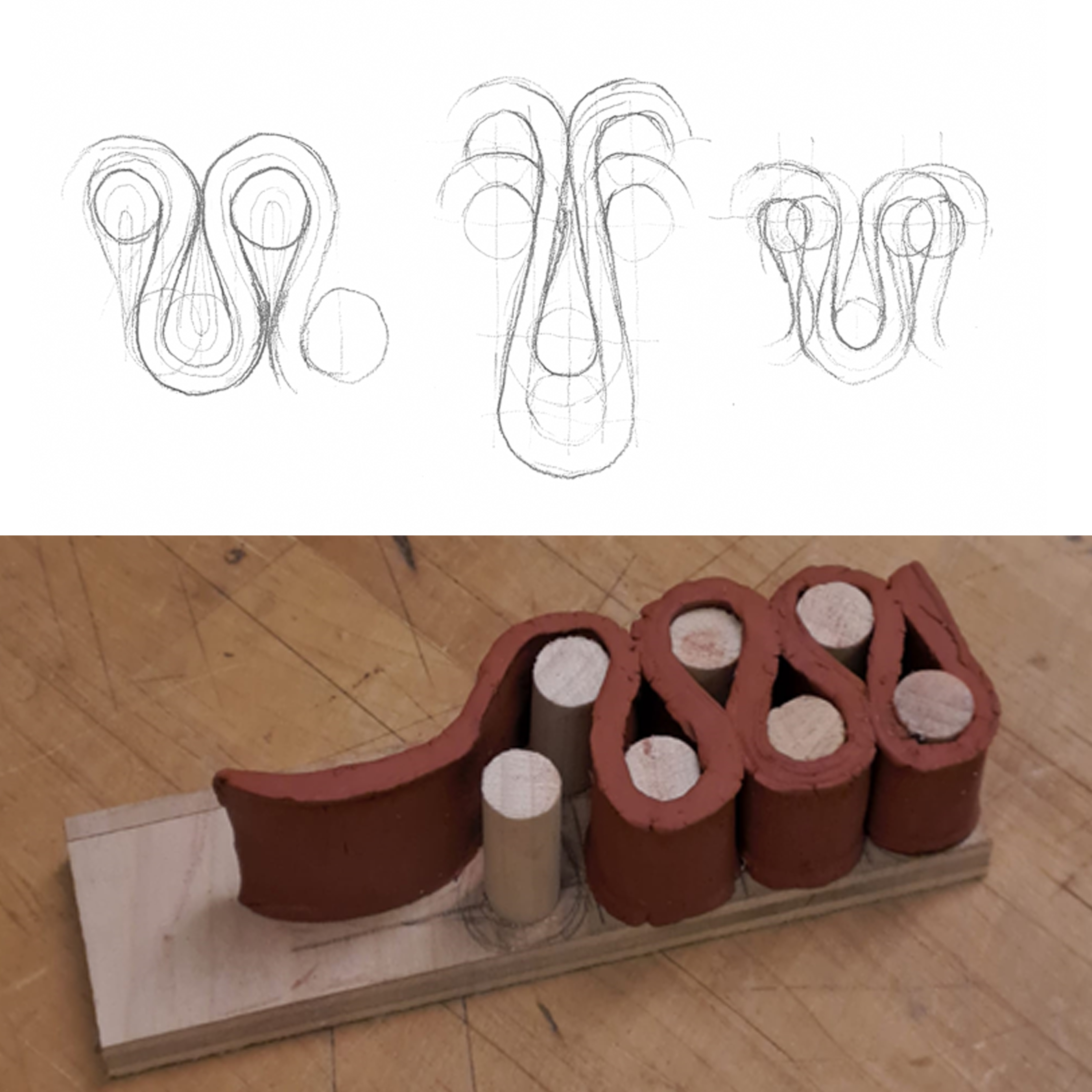
ADDITIVE ENERGY
2023
In this study, we ask if there are broadly scalable methods for additively manufacturing low-carbon, climate-specific architecture that are thermally and structurally performative for housing. We then demonstrate that high-performance, hierarchical building elements can be produced from extremely low-cost, low-carbon materials like earth using increasingly available 3D printing tools. We present a set of novel design methods and building systems from the scale of a brick to the scale of a wall, utilizing a combination of simulation-driven design and additive manufacturing with earth and clay. By leveraging materials readily available in all climates, bespoke, simulation-driven building elements could be manufactured from these low or no-cost materials to create performative, low-carbon buildings. By presenting a methodology for material and fabrication-aware energy simulation for additive manufacturing, this work provides scalable groundwork for future studies across climates and local building requirements.
Project team: Eduardo Gascon and Sandy Curth, Lawrence Sass, Leslie Norford, Caitlin Mueller
A free preprint of the research article can be found here.
Citation:
[1
A. Curth, E. Gascón Alvarez, L. Sass, L. Norford, and C. Mueller, “Additive Energy: 3D Printing Thermally Performative Building Elements with Low Carbon Earthen Materials,” 2024, pp. 28–45. doi: 10.1201/9781003403890-2.
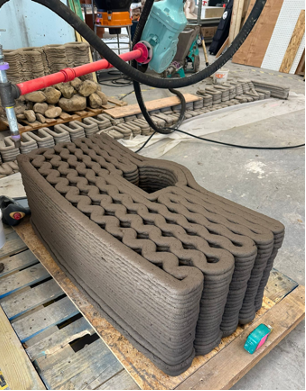


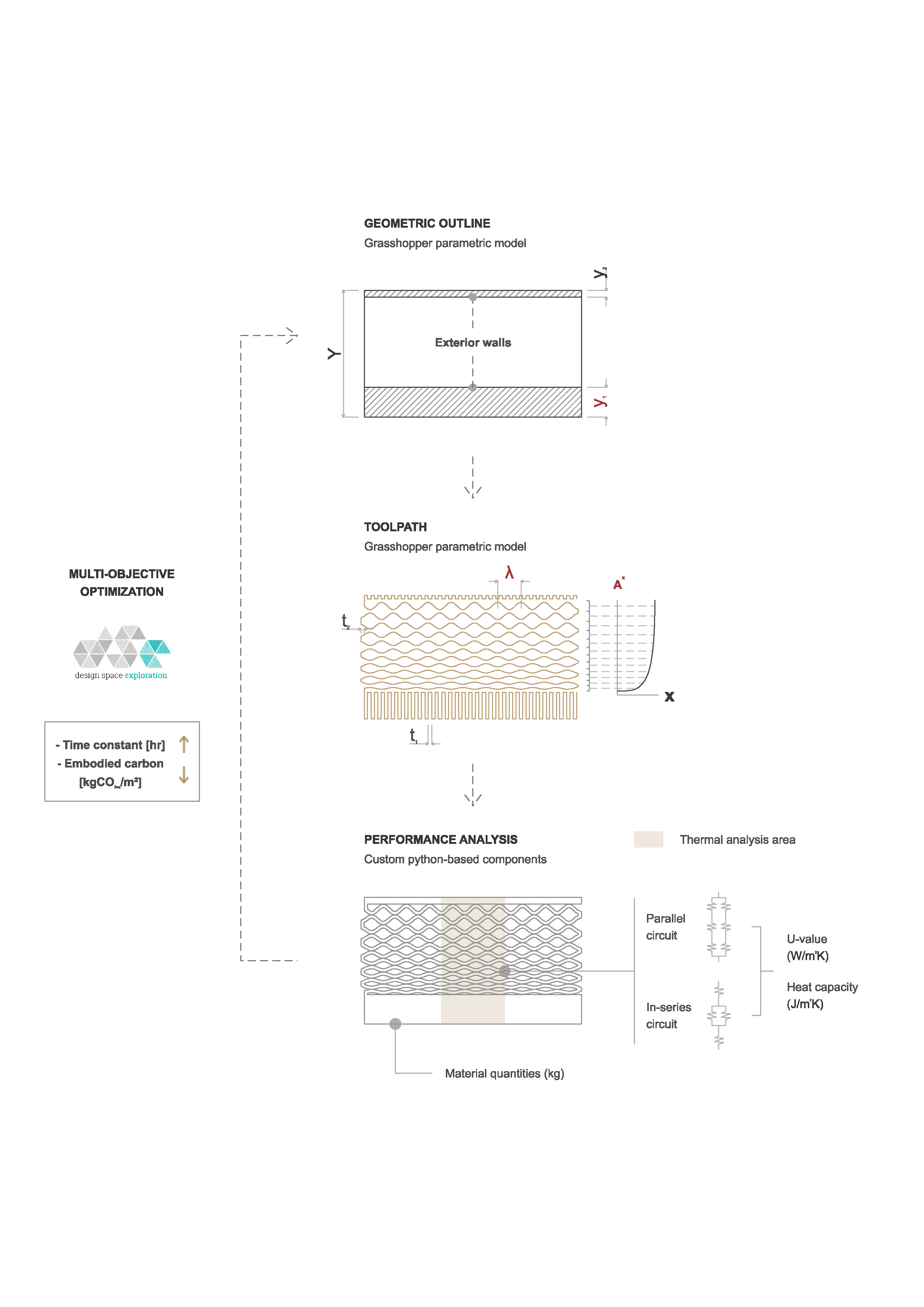
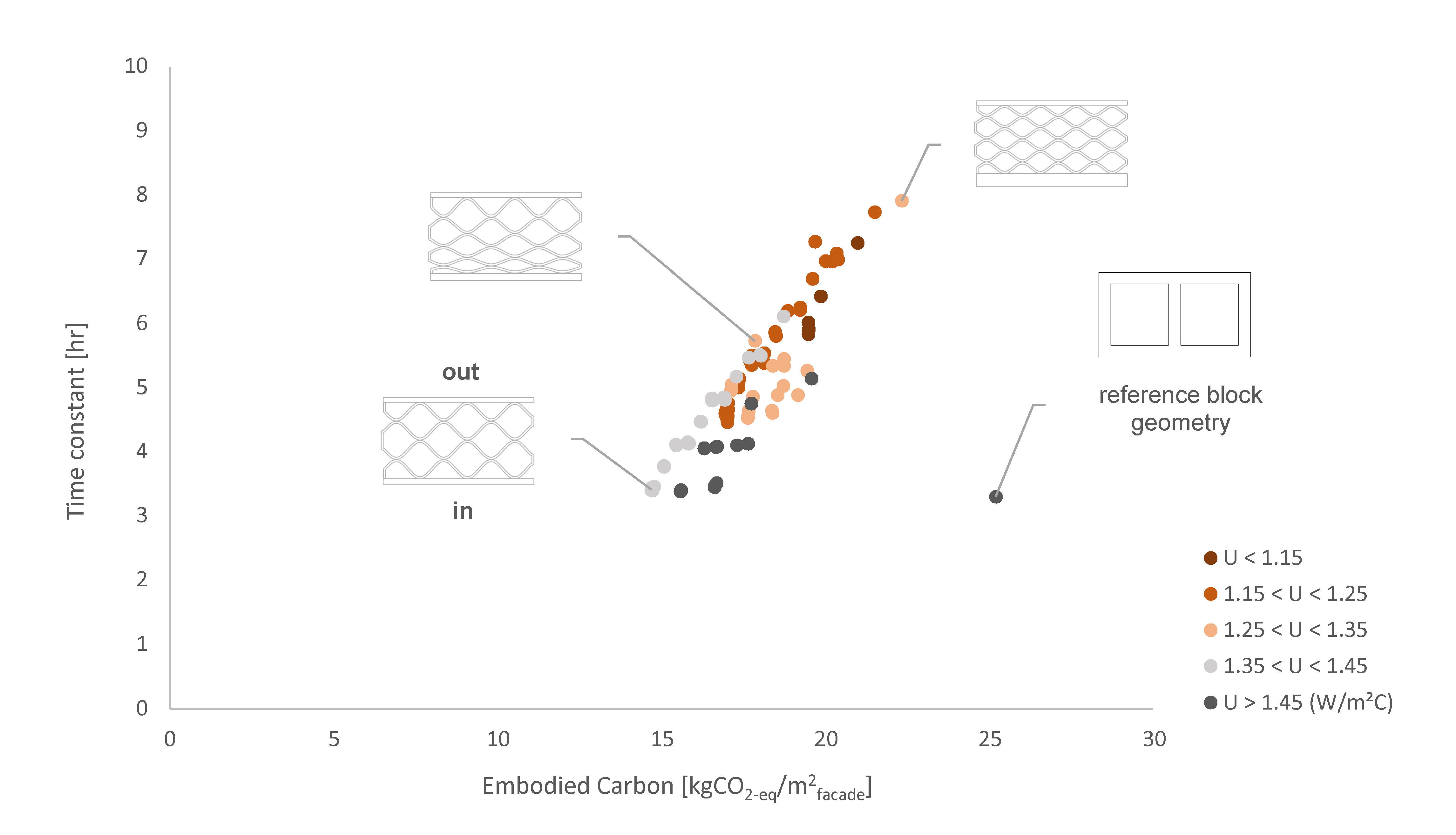
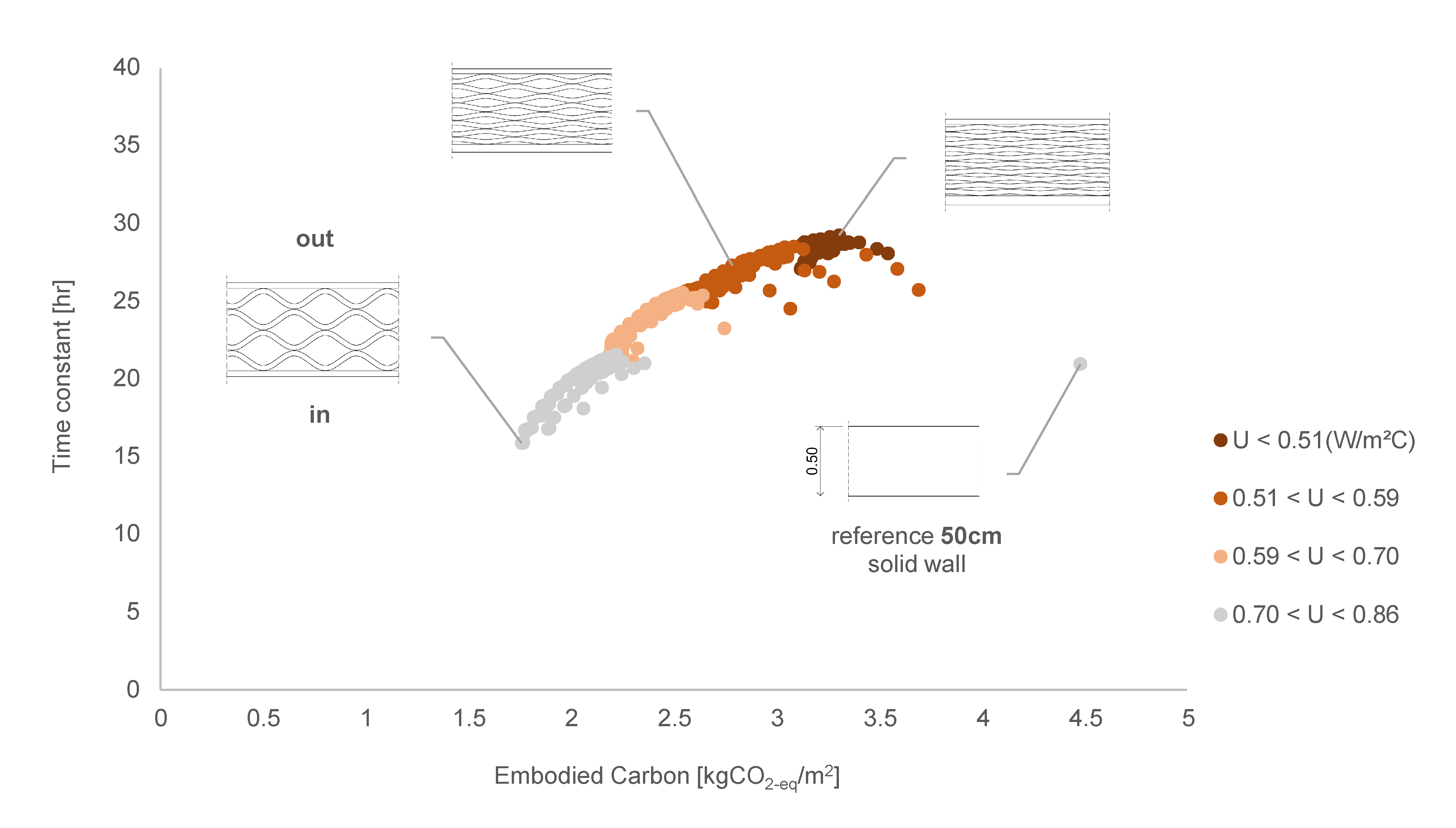
Mextropoli Sueños con Earth/Concrete
2022
Sueños con Earth/Concrete explores the future of affordable housing in Mexico by minimizing the material impact of existing construction methods. The horizontal roof structure takes the existing vigueta y bovedilla system as a starting point, optimizing the shape of the precast reinforced concrete beams to minimize the use of material and its associated environmental impact by 50% compared to conventional systems. This elegant geometry, sculpted by varying width and depth along the beam’s span, is enabled by recent computational design methods developed in MIT research. 3D-printed clay blocks vault between beams as lost formwork that enables the casting of a topping slab.The use of tepetate, a local soil with high contents of clay, allows for fabricating compressed, sun-dried blocks that constitute the pavilion walls. This affordable, low-carbon solution, which has been successfully applied in the construction of housing communities around Mexico for more than 30 years, is reinterpreted here with a post-tensioning system that allows for assembly and disassembly. Sueños con Earth/Concrete lies at the intersection of local construction techniques and new digital fabrication technologies, resulting in a collaboration between industry, social enterprise, and academia as a model toward a more sustainable built environment.
The geometric flexibility of 3D-printing facilitates the production of mass-customized ceramic block elements tailored to available materials and building design. Clay blocks are produced with local ceramic manufacturers using conventional clays and firing processes. The blocks themselves are lightweight and are optimized to minimize material usage and fabrication time.
Project team: Edu Gascón, Mohamed Ismail, Sandy Curth, Kiley Feickert, Caitlin Mueller, Leslie Norford.
In Collaboration with: ECHALE, New Story, Manufactura, Anfora Studio, Formas de Fibra de Vidrio.
Digital Structures MIT
News articles:
ArchDaily Sueños con Earth/Concrete
DesignBoom Sueños con Earth/Concrete
Open Access Publication here.
Citation:
[1]
A. Curth et al., “Sueños Con Tierra/Concreto: Multi-Material Fabrication for Low-Carbon Construction – an Optimised Floor System for Affordable Housing in Mexico,” in Fabricate 2024, in Creating Resourceful Futures. , UCL Press, 2024, pp. 214–221. doi: 10.2307/jj.11374766.31.



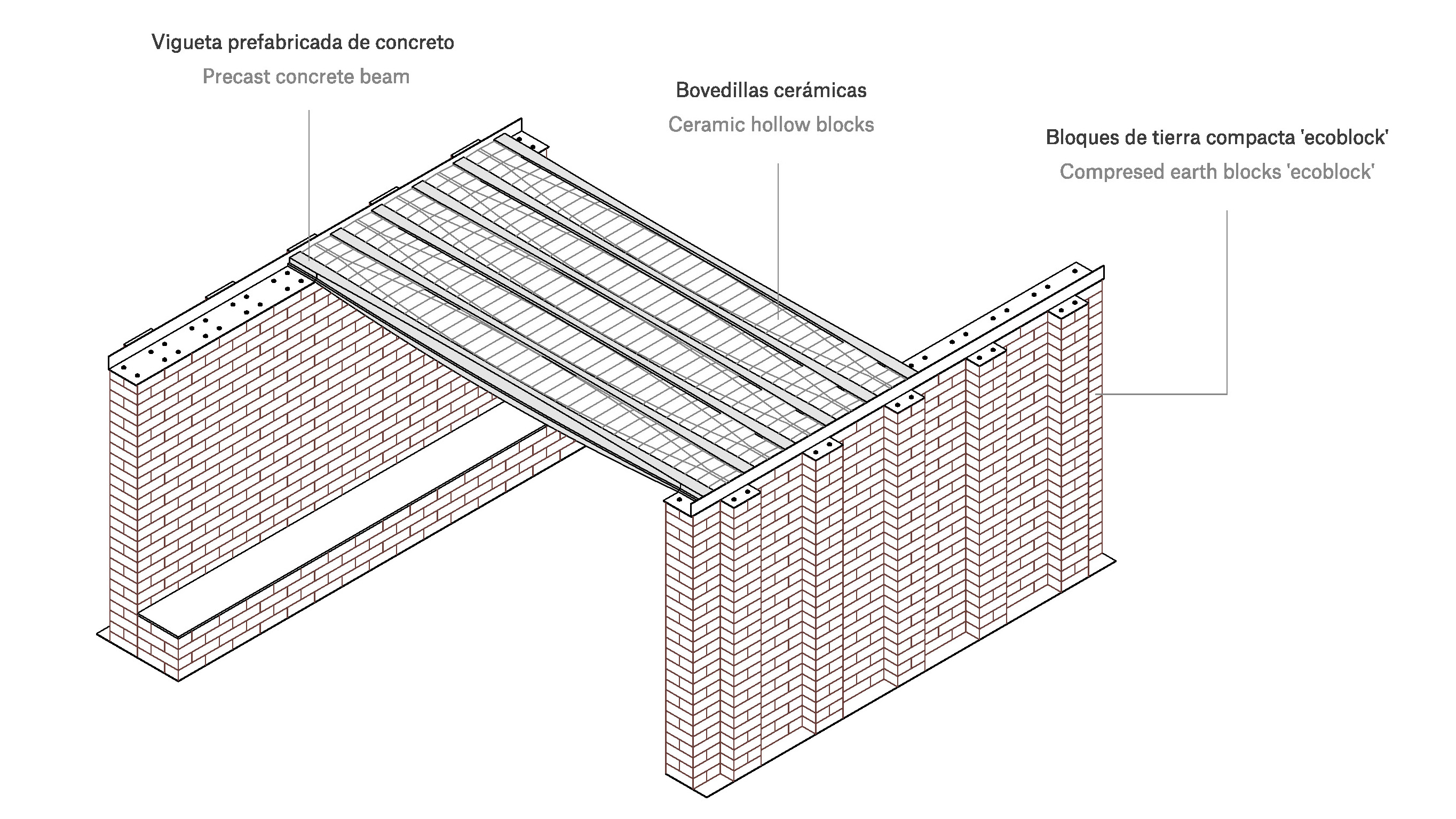
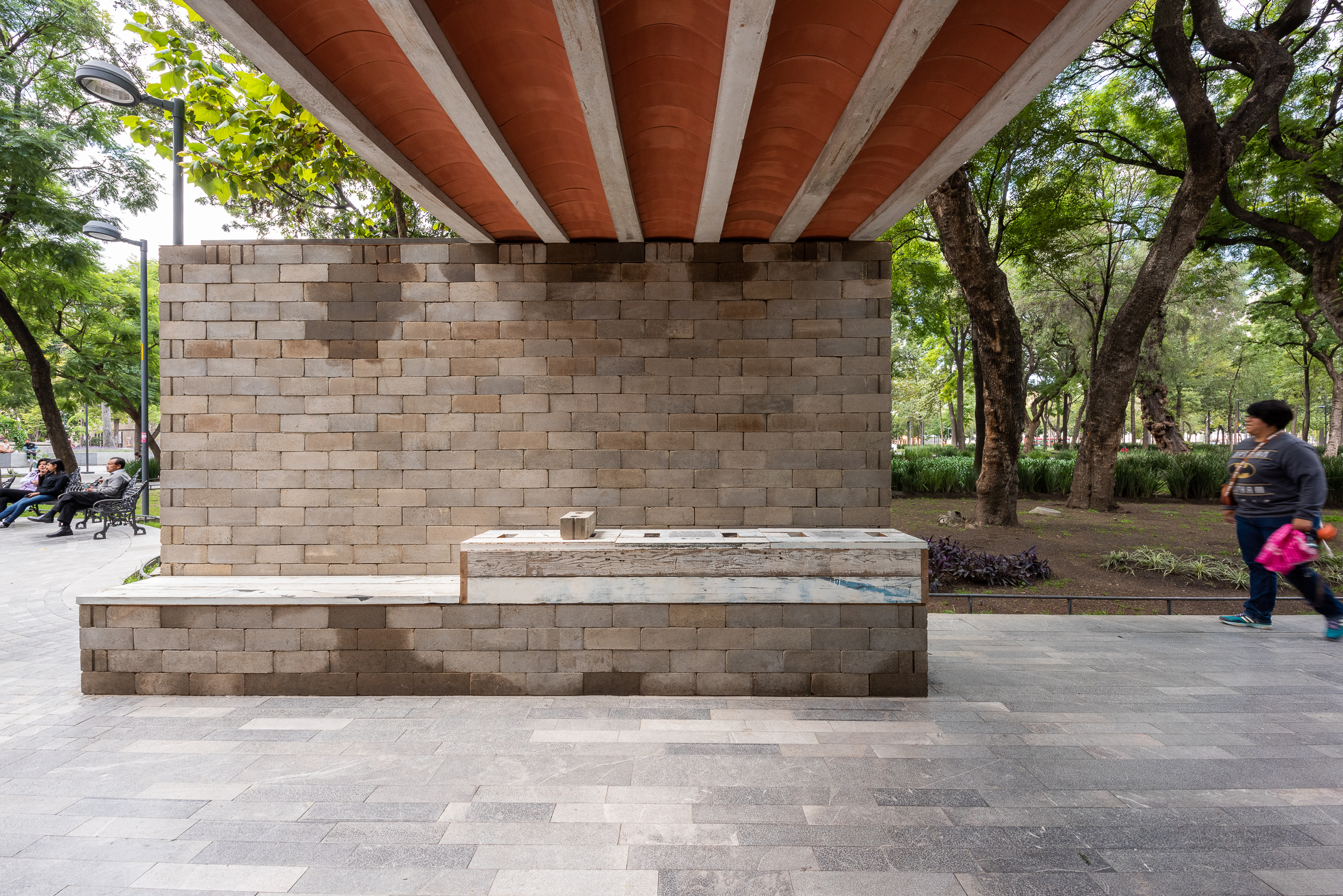


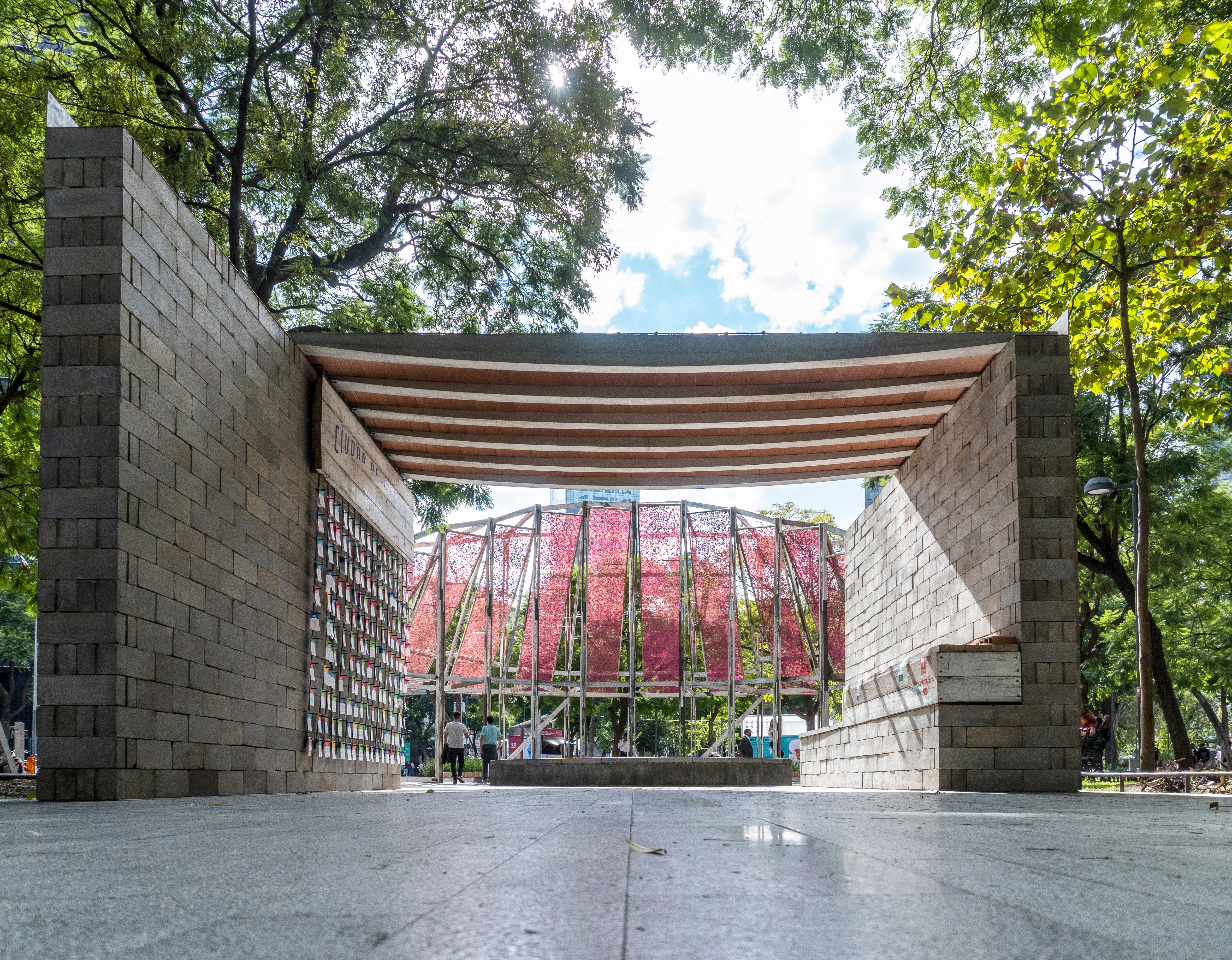
Earthworks // Tilt-Up
2022
EarthWorks explores the potential for excavation waste or other soils sourced directly from the construction site to be 3D printed into large-scale cast-in-place, prefab, or tilt-up formwork for reinforced concrete. Applications include carbon saving shape optimized structural systems, thermal and acoustically performative surface conditions, and radical geometric design freedom.
Here, we designed a portal frame using a 2D multi-objective shape optimization to minimize concrete while meeting design and code structural requirements. The 2D shape optimization approach taken here, while accessible and easy to use, is a numerical method that does not accurately model concrete mechanics, instead treating the concrete as an elastic material. This is in contrast to Case Study 3, in which a 3D-shape optimization model is used, taking into account the full mechanical behavior of reinforced concrete. The frame is fabricated on its side, a “tilt-up” casting strategy common in the site manufacturing of monolithic concrete walls for big-box stores and warehouses with sufficient staging areas. Here, the goal is to produce a materially efficient structural element, maximizing the working range of a single robot arm while keeping the fabrication time as low as possible. The formwork consists of a space-filling pattern on the ground plane, a printed extrusion of the frame’s 2D profile, and printed buttresses to manage the hydrostatic pressure of concrete during the casting process. The frame includes steel plates for bolted connections at its base and connection points for beams along its top. Once cured, the 3D-printed formwork is removed, and the frame is tilted into its upright position. Of the three methods tested, the tilt-up frame could be considered the most successful in that the ratio of material used in both the mold and the cast element is minimal, the rebar cage is conventional and straightforward to fabricate, and the final product is immediately ready for use as a structural component of a code compliant building. This is the fastest way to manufacture case studies while also being the largest single cast.
Project team: Sandy Curth, Natalie Pearl, Emily Wissemann, Latifa Alkhayat, Tim Cousin, Vincent Jackow, Moh Ismail, Caitlin Mueller
Open Access Publication here.
Citation:
[1]
A. Curth et al., “EarthWorks: Zero waste 3D printed earthen formwork for shape-optimized, reinforced concrete construction,” Construction and Building Materials, vol. 449, p. 138387, Oct. 2024, doi: 10.1016/j.conbuildmat.2024.138387.
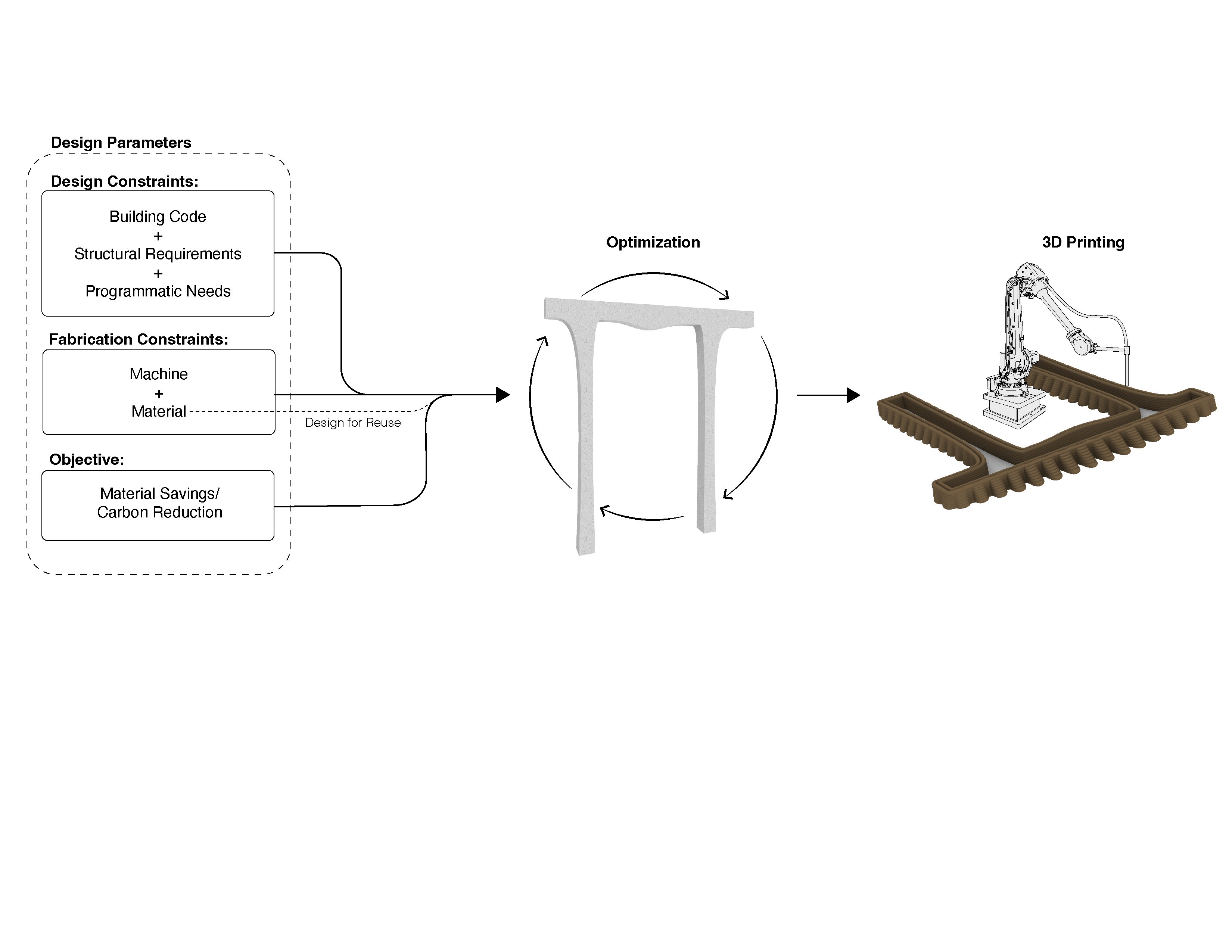
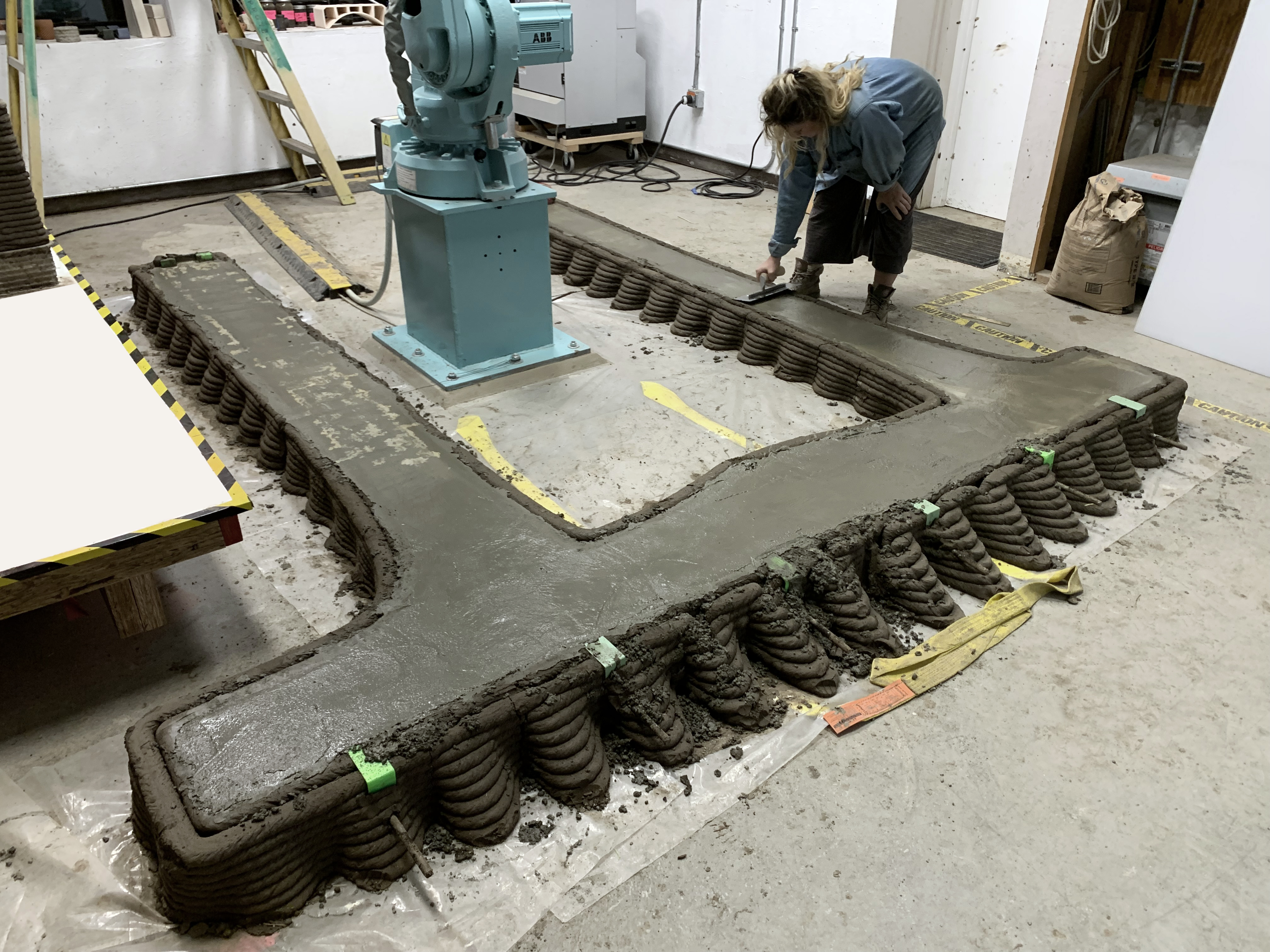


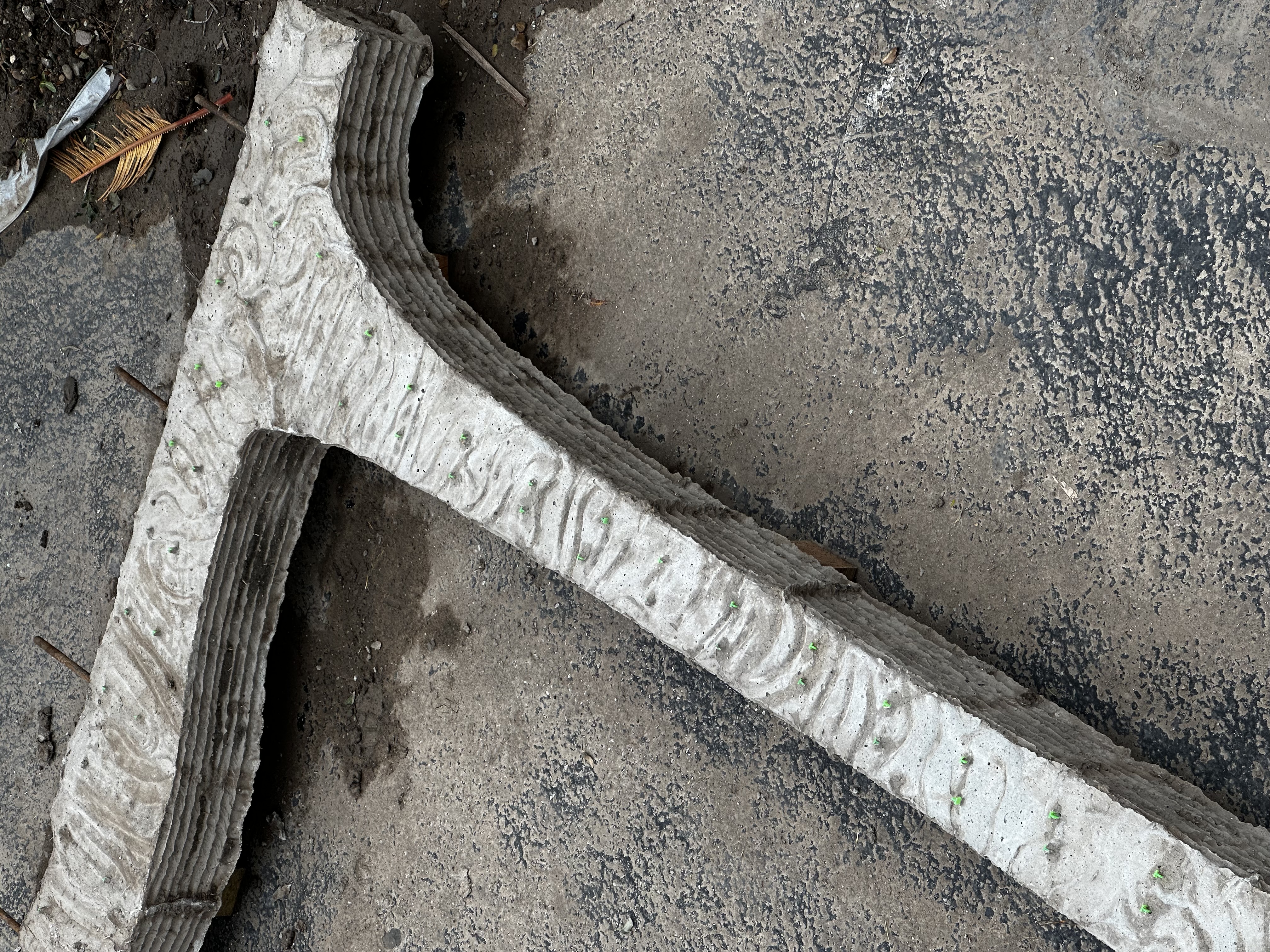

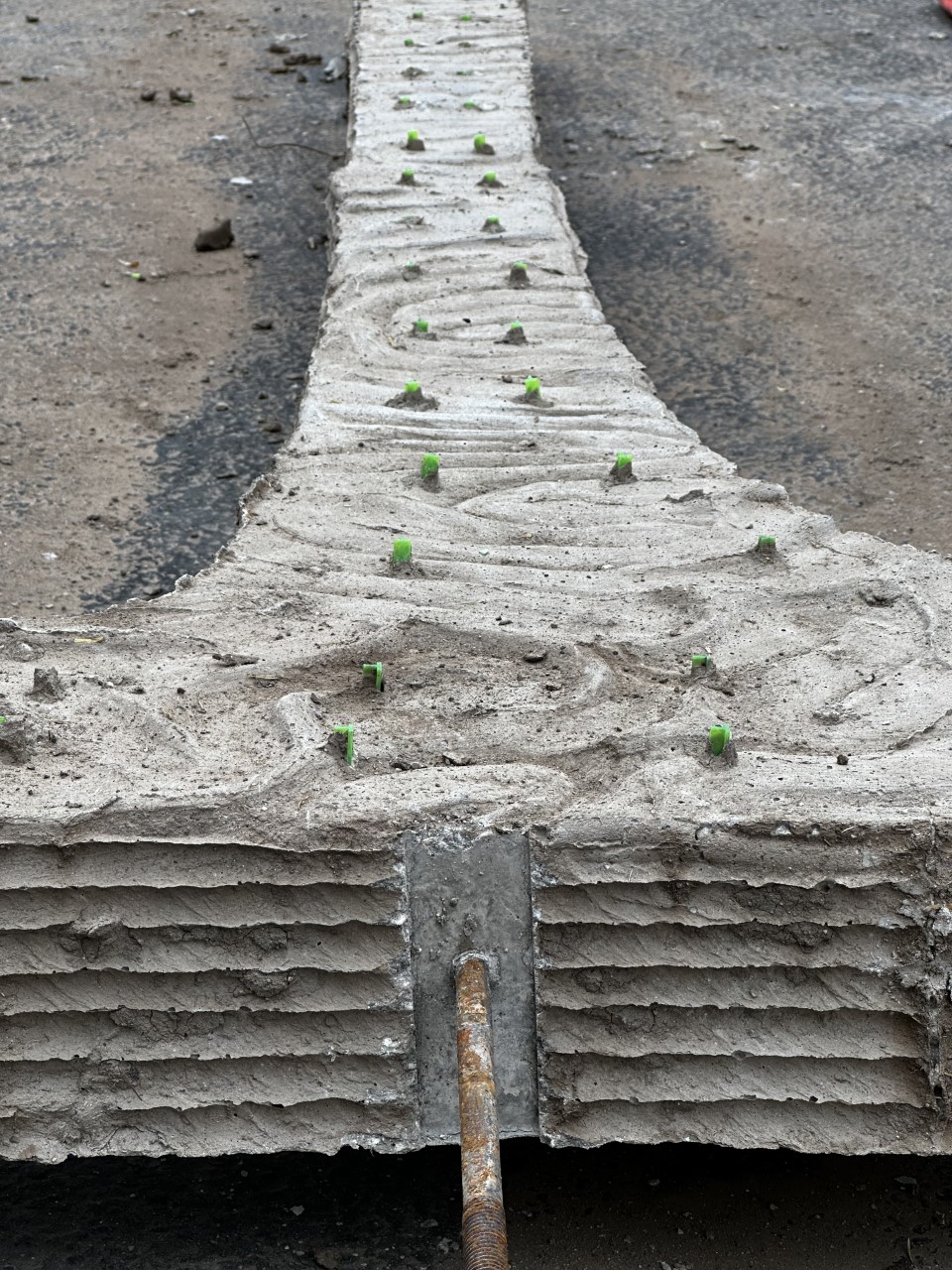




Earthworks // Pre-Fab Beam
2022
EarthWorks explores the potential for excavation waste or other soils sourced directly from the construction site to be 3D printed into large-scale cast-in-place, prefab, or tilt-up formwork for reinforced concrete. Applications include carbon saving shape optimized structural systems, thermal and acoustically performative surface conditions, and radical geometric design freedom. Here EarthWorks is used to generate zero waste molds for 3D shape optimized spanning elements like reinforced concrete beams.
Project team: Sandy Curth, Oliver Moldow, Natalie Pearl, Emily Wissemann, Latifa Alkhayat, Tim Cousin, Vincent Jackow, Moh Ismail, Caitlin Mueller
Open Access Publication here.
Citation: A. Curth et al., “EarthWorks: Zero waste 3D printed earthen formwork for shape-optimized, reinforced concrete construction,” Construction and Building Materials, vol. 449, p. 138387, Oct. 2024, doi: 10.1016/j.conbuildmat.2024.138387.

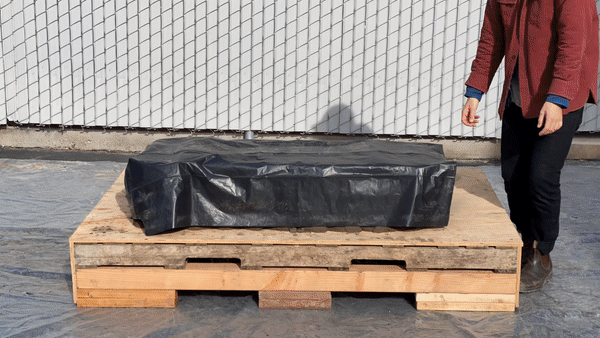

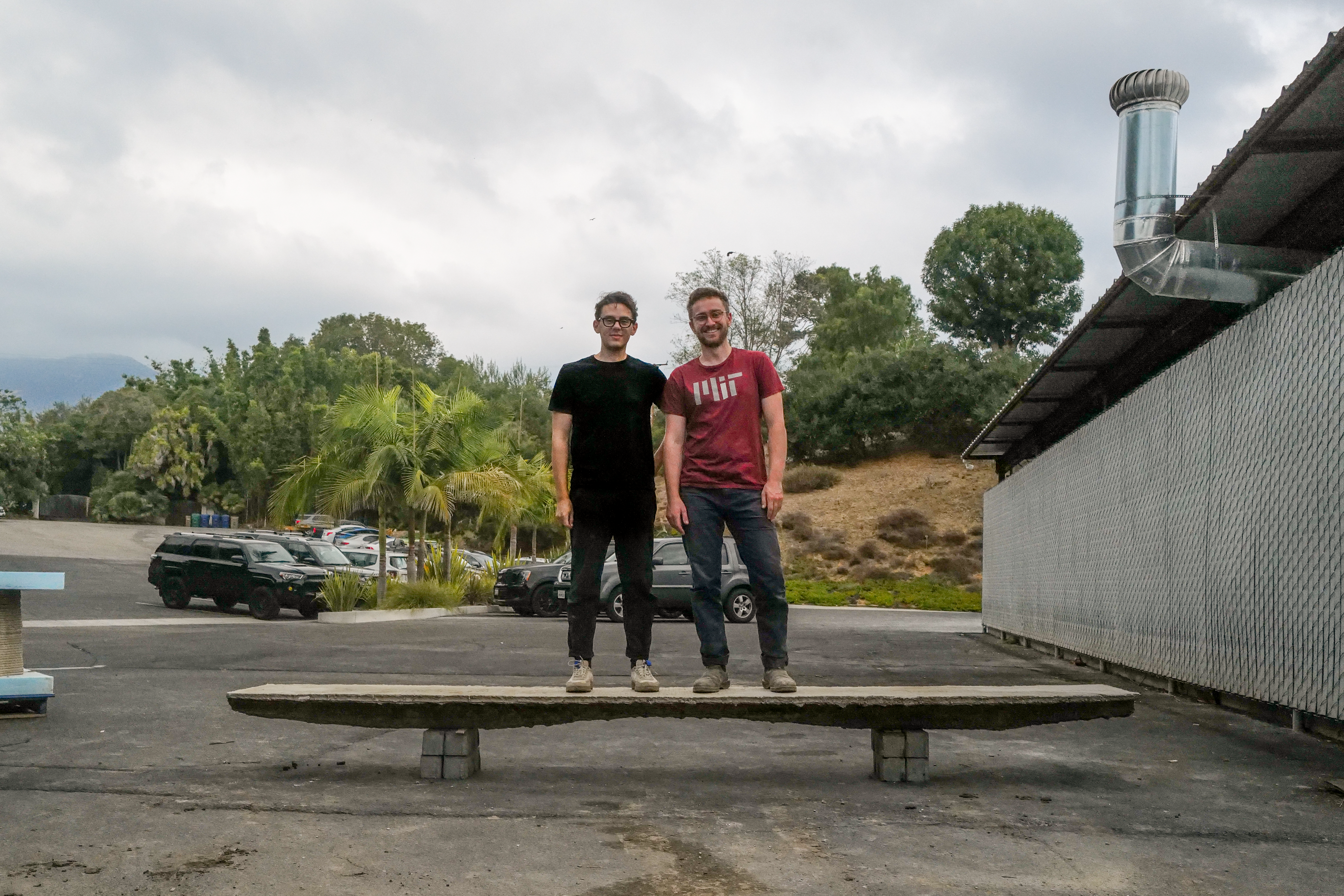
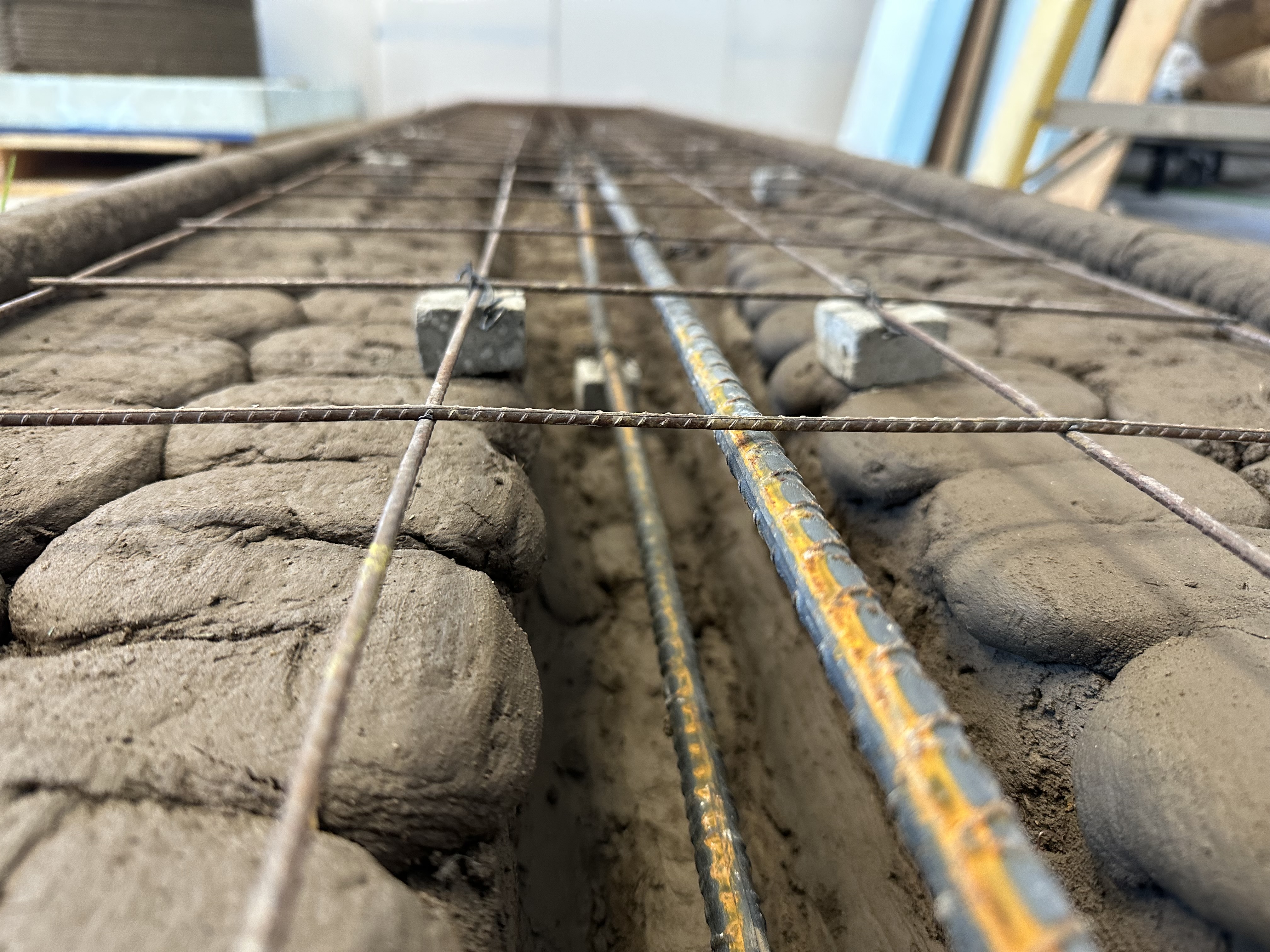

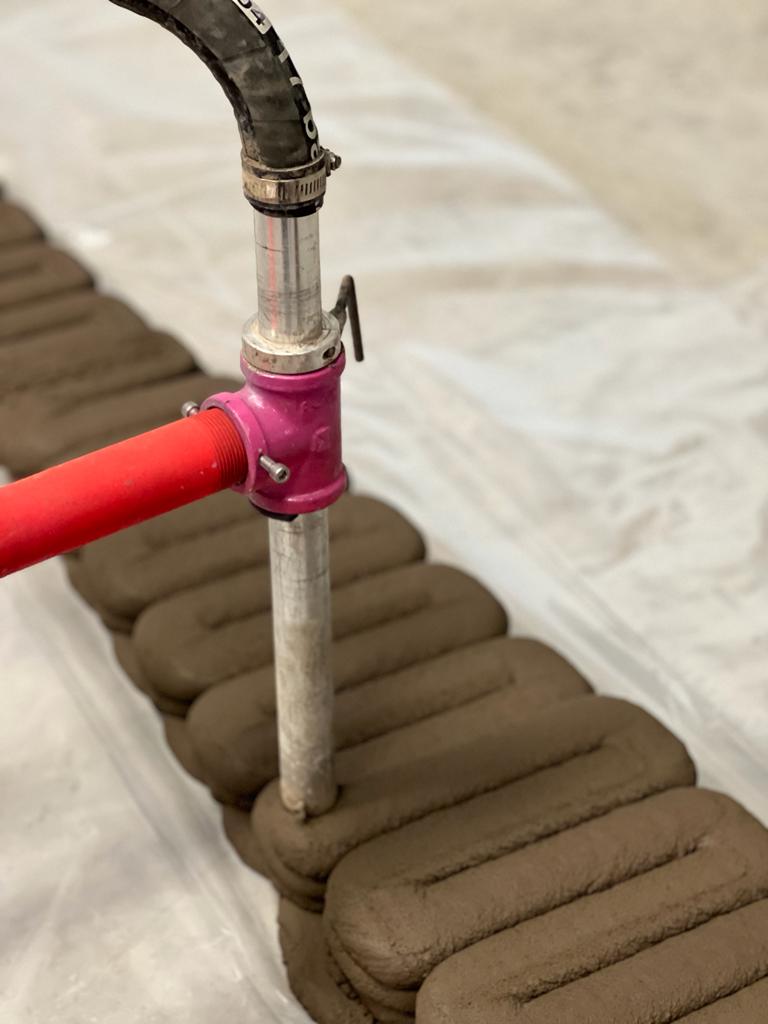
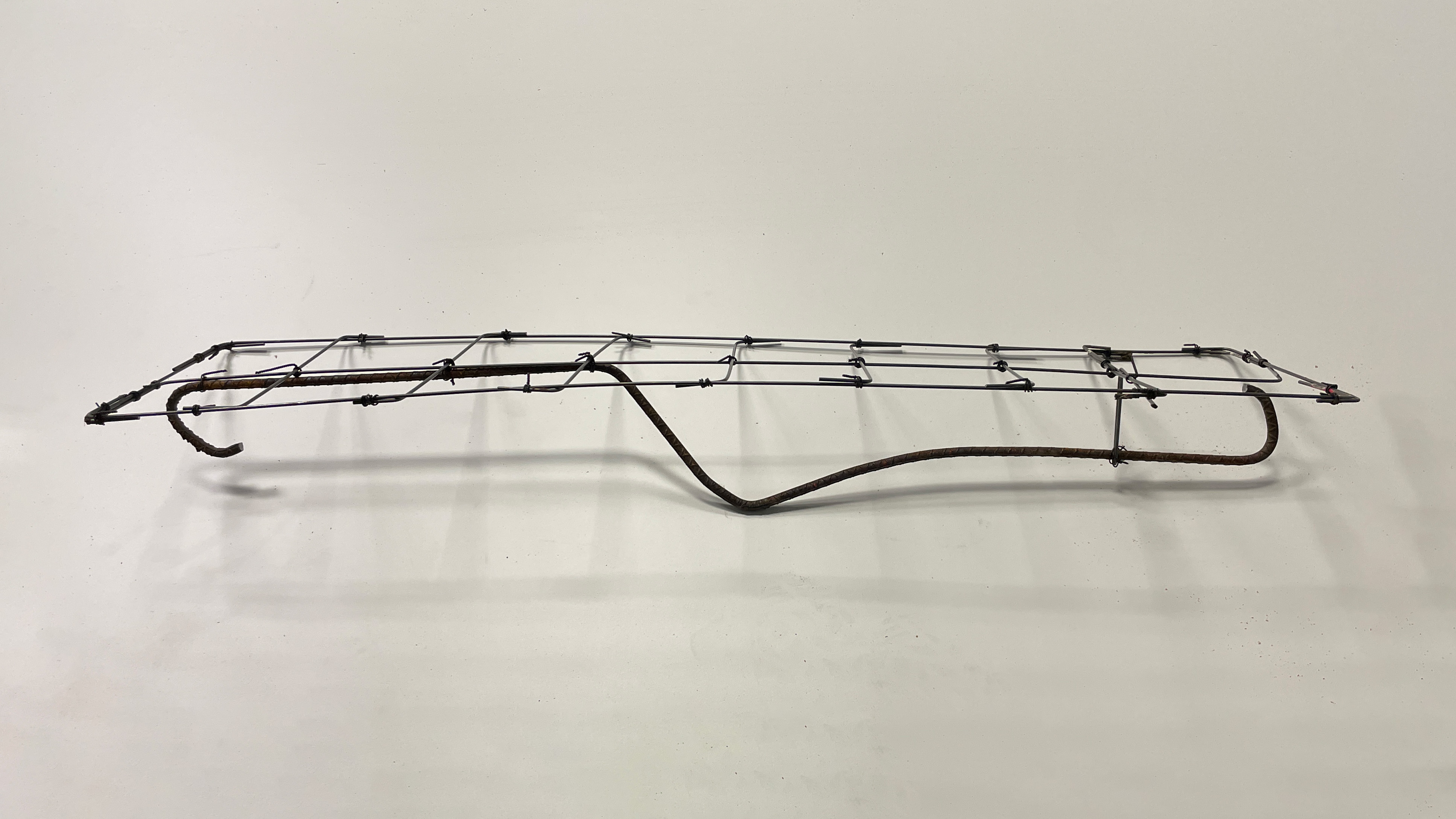
MIT Accessibility Information