Earthworks // Tilt-Up
2022
EarthWorks explores the potential for excavation waste or other soils sourced directly from the construction site to be 3D printed into large-scale cast-in-place, prefab, or tilt-up formwork for reinforced concrete. Applications include carbon saving shape optimized structural systems, thermal and acoustically performative surface conditions, and radical geometric design freedom.
Here, we designed a portal frame using a 2D multi-objective shape optimization to minimize concrete while meeting design and code structural requirements. The 2D shape optimization approach taken here, while accessible and easy to use, is a numerical method that does not accurately model concrete mechanics, instead treating the concrete as an elastic material. This is in contrast to Case Study 3, in which a 3D-shape optimization model is used, taking into account the full mechanical behavior of reinforced concrete. The frame is fabricated on its side, a “tilt-up” casting strategy common in the site manufacturing of monolithic concrete walls for big-box stores and warehouses with sufficient staging areas. Here, the goal is to produce a materially efficient structural element, maximizing the working range of a single robot arm while keeping the fabrication time as low as possible. The formwork consists of a space-filling pattern on the ground plane, a printed extrusion of the frame’s 2D profile, and printed buttresses to manage the hydrostatic pressure of concrete during the casting process. The frame includes steel plates for bolted connections at its base and connection points for beams along its top. Once cured, the 3D-printed formwork is removed, and the frame is tilted into its upright position. Of the three methods tested, the tilt-up frame could be considered the most successful in that the ratio of material used in both the mold and the cast element is minimal, the rebar cage is conventional and straightforward to fabricate, and the final product is immediately ready for use as a structural component of a code compliant building. This is the fastest way to manufacture case studies while also being the largest single cast.
Project team: Sandy Curth, Natalie Pearl, Emily Wissemann, Latifa Alkhayat, Tim Cousin, Vincent Jackow, Moh Ismail, Caitlin Mueller
Open Access Publication here.
Citation:
[1]
A. Curth et al., “EarthWorks: Zero waste 3D printed earthen formwork for shape-optimized, reinforced concrete construction,” Construction and Building Materials, vol. 449, p. 138387, Oct. 2024, doi: 10.1016/j.conbuildmat.2024.138387.
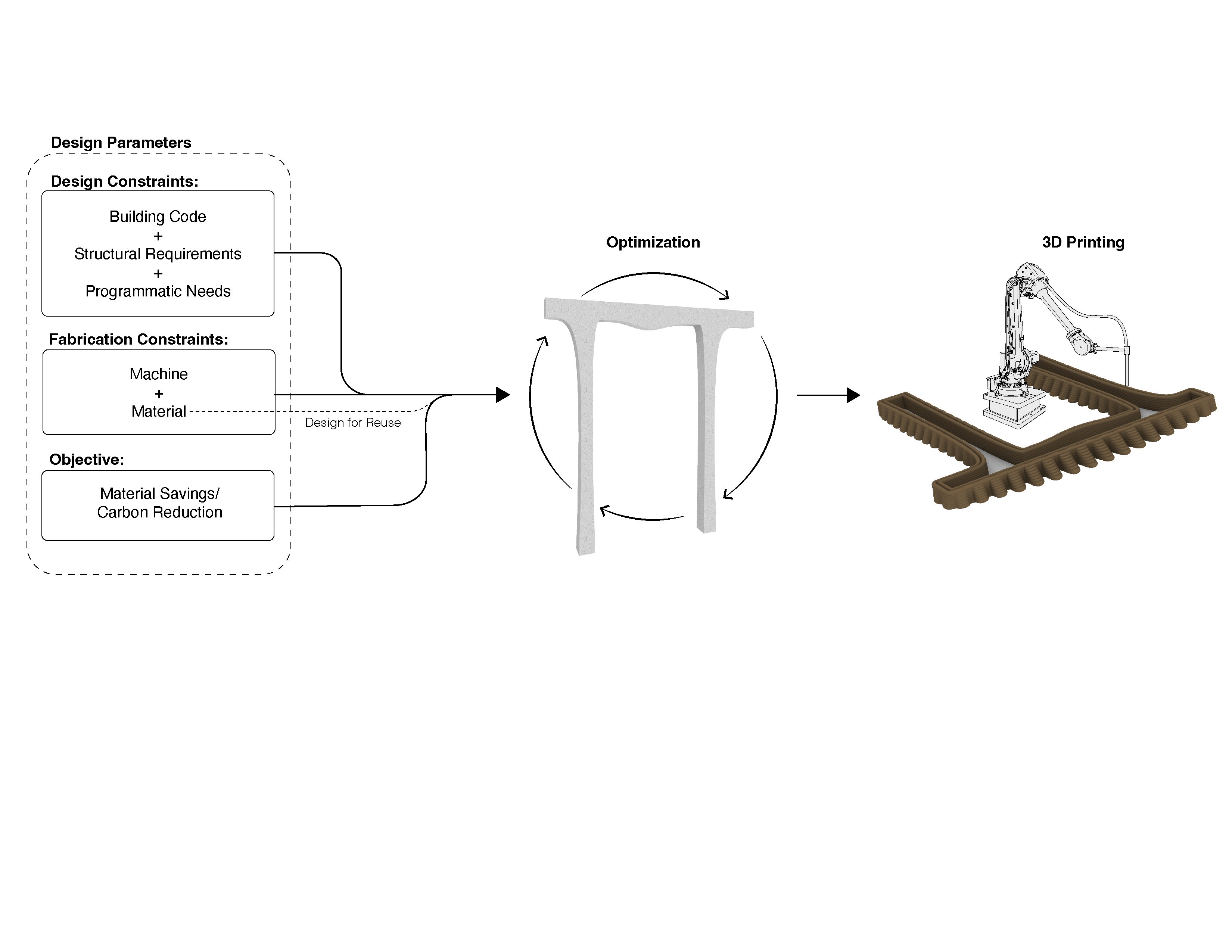
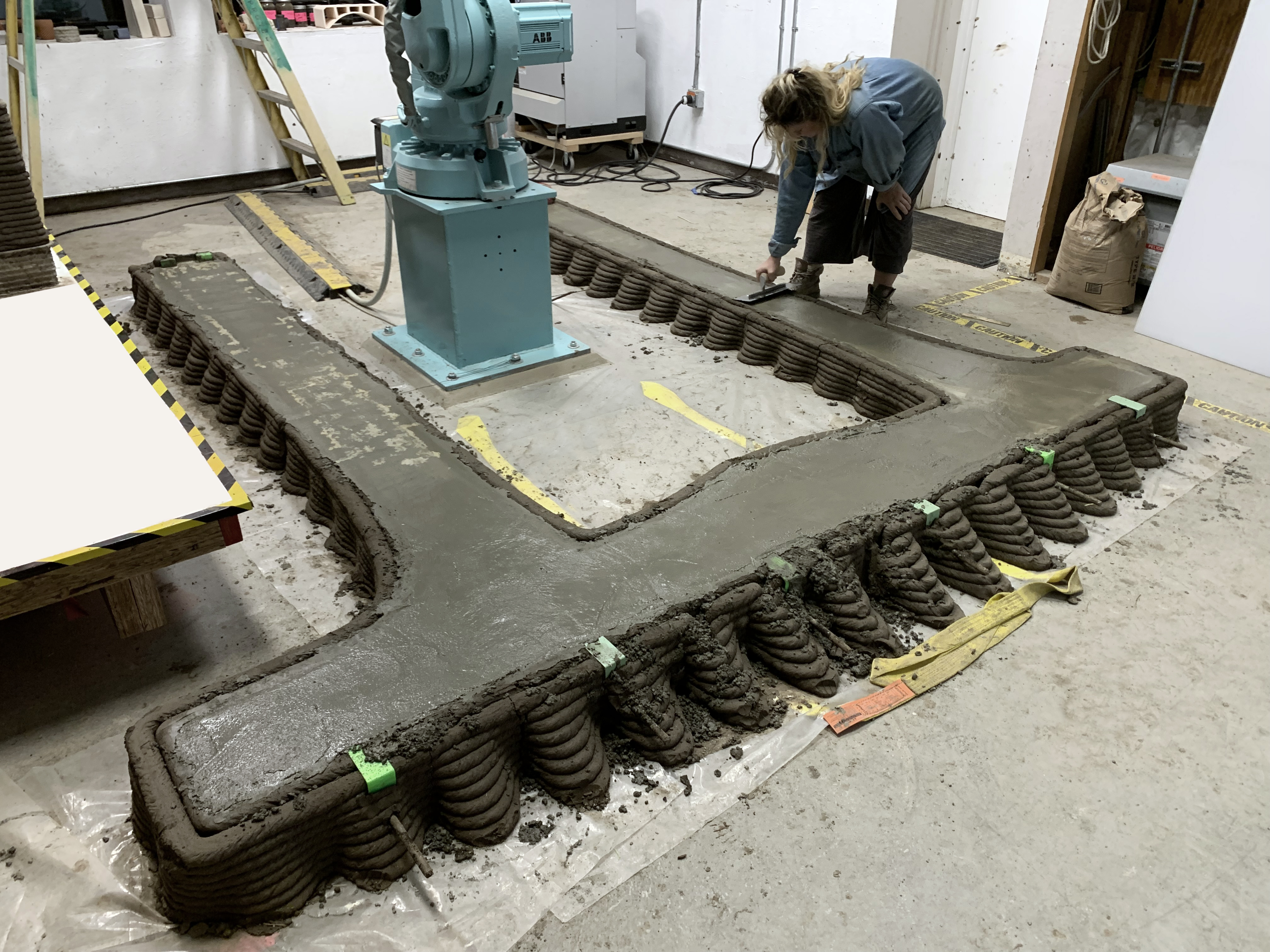


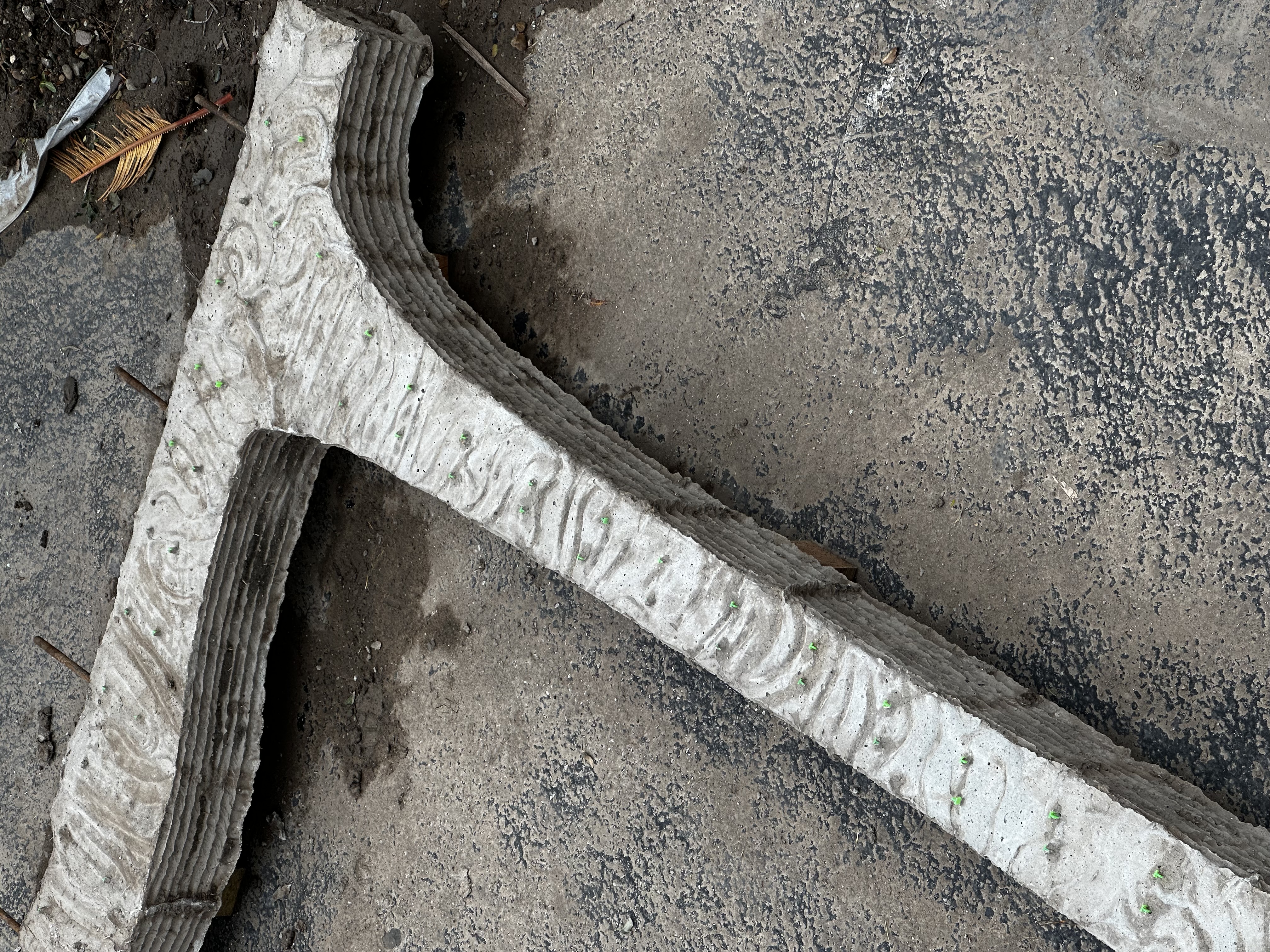

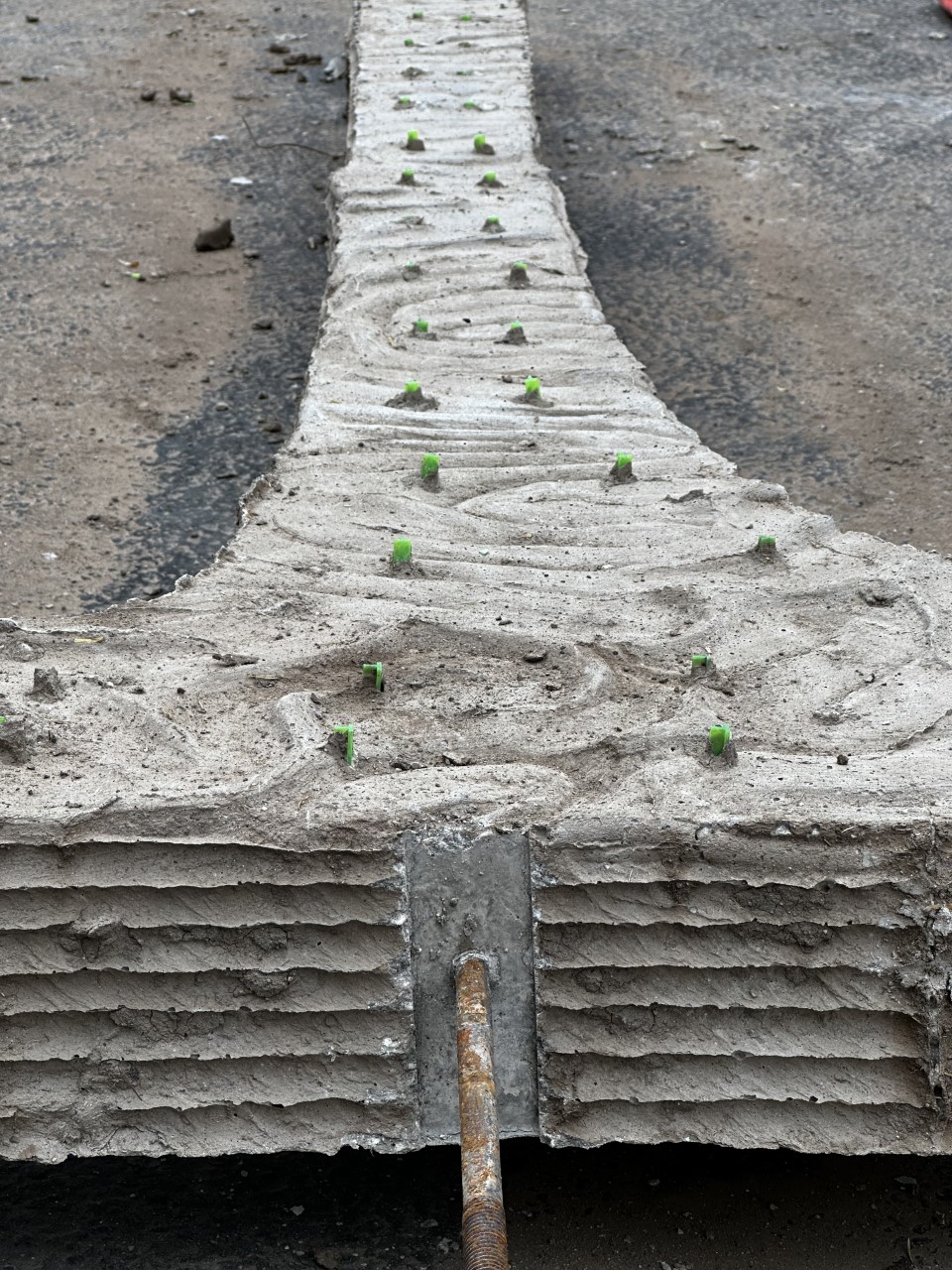




MIT Accessibility Information